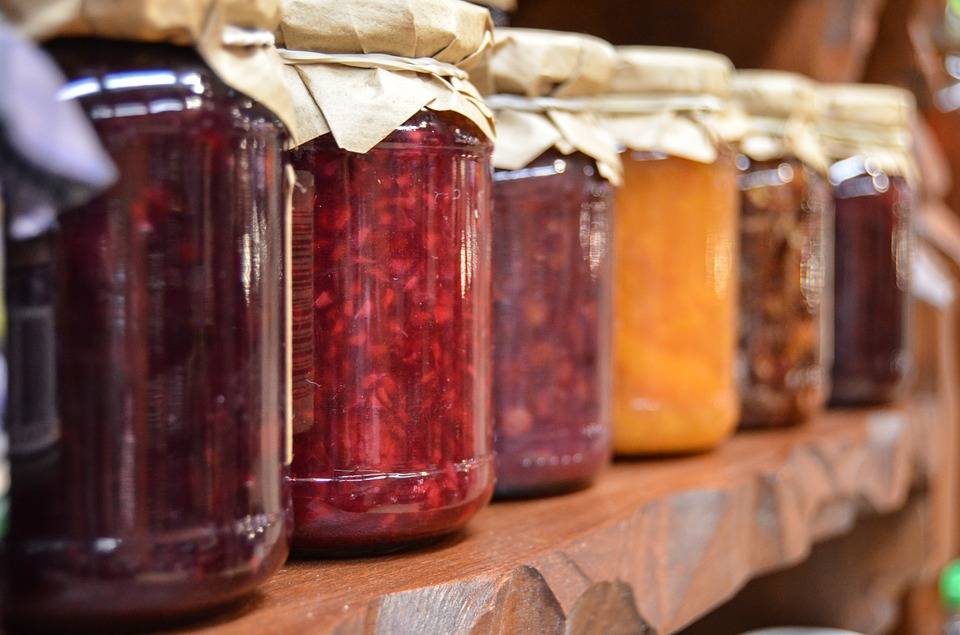
The modern food industry produces a wide range of products made from fruits and berries such as preserves and jam, jelly and marmalade, and grated and crushed berries. At the heart of all this diversity are preservative properties of high concentrations of sugar. When the amount of sugar is between 60 to 65%, sugar syrup creates a high osmotic pressure, whereby the microorganisms get dehydrated and perish. If the final product contains more than 65% of solids, it can be stored for a long time without pasteurization. However, on an industrial scale only fruit paste is produced without pasteurization because during storage of preserve, jam, and other products with sugar syrup, moisture can accumulate in the upper layer, thereby reducing sugar concentration and allowing for fermentation.
Fruit preserves. Fruit preserves have the most sophisticated production technology. This product consists of sugar syrup and a fruit/berry that has retained its shape during boiling. To obtain high-quality preserves you need to heat fruits/berries repeatedly and continuously, so that you could save the marketable condition of the fruits/berries. Herewith, the kind and maturity degree of fruits/berries are of great importance. If fruits or berries have not reached maturity – fruit preserves can become gelatinous due to the high content of protopectin, and overripe fruits or berries will simply fall apart while cooking.
Briefly, the technological process of cooking fruit preserves is as follows: after preparing (sorting, removing the stalks, seeds, and other) raw materials are blanched in hot water for a few minutes to soften the pulp and increase permeability. If fruits and berries have been conditioned with sulfur (sulfurizing) to improve their storage capabilities, then they are to be pre-desulfurized by boiling.
Syrup is prepared from sugar (sometimes adding 15% of molasses to reduce the risk of crystallization of the product). If sulfurized raw material is used – sugar is added into the solution, remained after desulfurization, that has been passed through a filter.
Traditionally, fruit preserves are prepared in special cooking boilers equipped with a steam jacket for heating the raw material, and a paddle stirrer. Since fruits and berries are put into syrup with a high sugar concentration, diffusion of water from fruits into syrup goes faster than the reverse diffusion of syrup. This can lead to, if the cooking conditions are violated, berries become wrinkled, hard and start to floating. Preliminary blanching, pricking or rolling partially weaken the peeling and mutual diffusion of water and syrup goes more evenly. Multiple boiling with intermediate cooling (from 10 to 24 hours) improves soaking of the raw material with syrup because, while cooling, the reduced pressure starts to build up inside fruits and therefore syrup penetrates the peeling much better. The duration of one boiling varies from 10 to 15 minutes, and the total boiling time should not exceed 30 minutes.
It is much more effectively and quicker to cook fruit preserves in a vacuum apparatus. In fact, such an apparatus is the same cooking boiler with steam heating and a paddle stirrer, but in addition to that it is equipped with a seal cap and a vacuum pump. Feedstock is cooked in a vacuum unit under the reduced pressure for 10-15 minutes, and then is cooled under the increased pressure for 10 minutes. Straight after that, the pressure is reduced again and boiling continues for the second time.
During the process of cooking fruit preserves the solids content in syrup is continuously monitored. The weight of solids in the finished product (after sugar completely diffuses into fruits) should be in the range of 68-70% (including the weight of fruits and berries at 40-55%).
There is an increased demand on the market for gelatinous products made from processed fruits and berries, such as jam and jelly. Requirements for the raw material for their preparation are higher than for preserves. Ideally, fruits and berries should contain more than 1% of pectin and at least 1% of organic acids. If there is not enough pectin in the raw material, then it is added as a dry powder or jellifying juices out of gooseberry, quince, or apple.
Jam is prepared in a cooking boiler or a vacuum unit, equipped with a paddle stirrer. The preparation technology provides for a single cooking with boiling until the concentration of solids reaches to 69-73%. Prepared fruits or berries are loaded into the machine, fill with water or a mild (10%) sugar syrup and blanch until the raw material gets soft. Then a concentrated sugar syrup or sugar is added and the cooking process continues until ready. Jellifying juice is added into the vessel 15-20 minutes before the end of boiling. In order to prevent jam from becoming crystallized during storage, it is added with the citric acid or 15% of sugar in syrup is substituted with molasses.
Jelly differs from jam by a more dense consistency and the presence of small pieces of fruits. For its preparation vessels are used with the capacity of not more than 150 liters. During the process of cooking, when the concentration of solids is about 55%, pectin is introduced into the feedstock and the process continues until the concentration of solids in syrup reaches about 60%. Boiling is done pretty fast (up to half an hour), due to which the product better preserves the vitamins, flavor and the aroma of fruits. Citric or tartaric acid is added into the vessel a couple of minutes before the end of cooking, bringing the concentration of acid in jam up to 0.8-1.3%.
Fruit paste is produced by boiling the pre-prepared puree with sugar in a cooking boiler or a vacuum unit equipped with a paddle stirrer. Fruit paste has a jelly-like consistency and a sour taste, which is due to the addition of pectin and citric acid (tartaric acid) into puree. If fruit paste is prepared from a sulfited feedstock, then puree has to be pre-boiled without sugar until the solids concentration gets to 15%, whereupon you add sugar in the amount determined by the recipe and continue boiling till the product is ready. If the initial puree has a thick consistency, it is boiled with half amount of sugar till the solids concentration is 45%, and then you add the remaining sugar and proceed until the product is ready. If liquid puree is used as a raw material, then puree and the whole amount of sugar are poured into the cooking vessel simultaneously. The cooking time of fruit paste should not exceed 50 minutes. Exceedance of this limit will impair the quality of the final product.
If a vacuum apparatus is used, puree with sugar is warmed up at atmospheric pressure for a few minutes, then cook at the reduced pressure until done. If the raw material requires desulfurization, it is first pre-conditioned in open apparatuses, then sugar is dissolved and the substance is brought to boiling, after which boiling continues under the reduced pressure until ready.
At the end of the jam cooking process the pressure in the vacuum unit is increased to the atmospheric for a short period of time, and the temperature is brought to 1000С.
The quality of the finished products equally depends on the quality of raw materials and equipment being used. The GlobeCore food containers are made of high-quality stainless steel and equipped with reliable paddle mixers. Small containers with a capacity of 100-300 kg per cycle are intended for the production on a small or medium scale, or testing recipes at large enterprises. For a large production available cooking vessels with a capacity up to 5000 kg/cycle. The GlobeCore equipment stands out for its high efficiency, small technological losses of raw materials, small time spent on cleaning the vessels, and a low energy consumption.