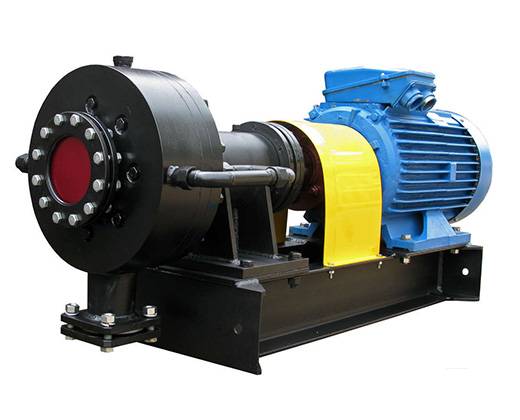
Colloid Mills. Colloid pulverization is such processing of materials which produces partices of colloidal sizes (several micron and smaller).
At certain conditions, this degree of pulverization can be achieved with just about any industrial grinding equipment. But if the process is considered from the economic and technological viewpoints, it becomes apparent such tasks are best performed by colloid mills. There is no coagulation of particles in the colloid mills, since the process occurs in dispersing media (liquids or, seldom, gases).
Colloid pulverization is almost always a “wet” process. The ratio of solid and liquid phases varies with the nature of the material and can be anywhere from 1:2 to 1:6.
Colloid solutions, unlike normal ones, are heterogeneous. Colloid particles have sizes much larger than the molecules of the dispersion media, which causes formation of phase boundary between liquid and solid phases. The height of this surface increases with increased dispersion of the material.
GlobeCore presents the CLM colloid mills for food, road construction, chemical and other industries. This product is designed specifically for fine pulverization of materials and production of highly stable suspensions, emulsions and solutions. Passing through the gap between the rotor and the stator of the mill, product particles rotate. Centrifugal force tears the particles apart. There are other effects, such as cavitation, which facilitate high quality of dispersion and homogenization.
The CLM colloid mills feature the following advantages:
- adjustment of pulverization degree and pumping characteristics;
- production of highly stable materials at the required rate;
- high degree of homogenization;
- production of colloid mills from carbon steel, food grade stainless steel or chemically resistant stainless steel on customer request;
- the mills can be equipped with general purpose or intrinsically safe motors depending on production conditions.