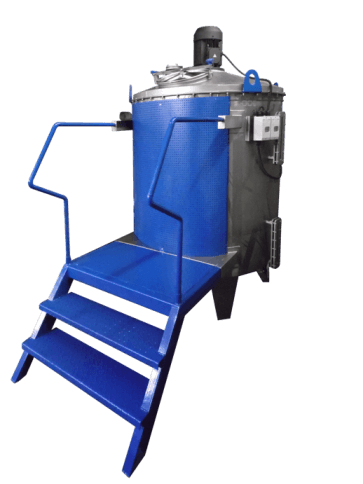
Laboratory equipment, despite its apparent simplicity, plays a crucial role in industrial processes.
To understand this, recall the whole process of designing machines and mechanisms for the production of consumer products, from the beginning. In the first stage a prototype of the equipment is produced, which is then subjected to all kinds of tests, simulating the situations that may arise during industrial operation.
Homogenizers are used for a homogeneous distribution of one substance in another. They are used in such industries as food, chemical and pharmaceutical manufacturing. In the food industry homogenizers determine the consistency, structure, color, and finally, the palatability of the product. Pharmaceutical and chemical industries also cannot do without homogenizers, because homogenizers affect the speed of reactions in the preparation of suspensions and emulsions.
Laboratory homogenizers are used in the same areas as the industrial ones, but they work with small amounts of substances. As noted above, they are necessary for simulation of industrial production, formulation of new recipes, as well as research.
GlobeCore manufactures a CLM laboratory homogenizer (colloid mill) with the processing capacity up to 1.8 m3 / hour. Unlike its “big brothers”, a laboratory version of the CLM has a compact design (720/700/1330 mm). Depending on the characteristics of the future use of the device it can be made of chemically resistant stainless steel, black metal or stainless steel.
The operating principle of laboratory homogenizers GlobeCore is based on the centrifugal force and the high relative velocity between the rotor and the stator, achieving homogeneity of semi-liquid materials.
CLM homogenizers’ great advantage is that they can also disperse the processed products in the process of homogenization.