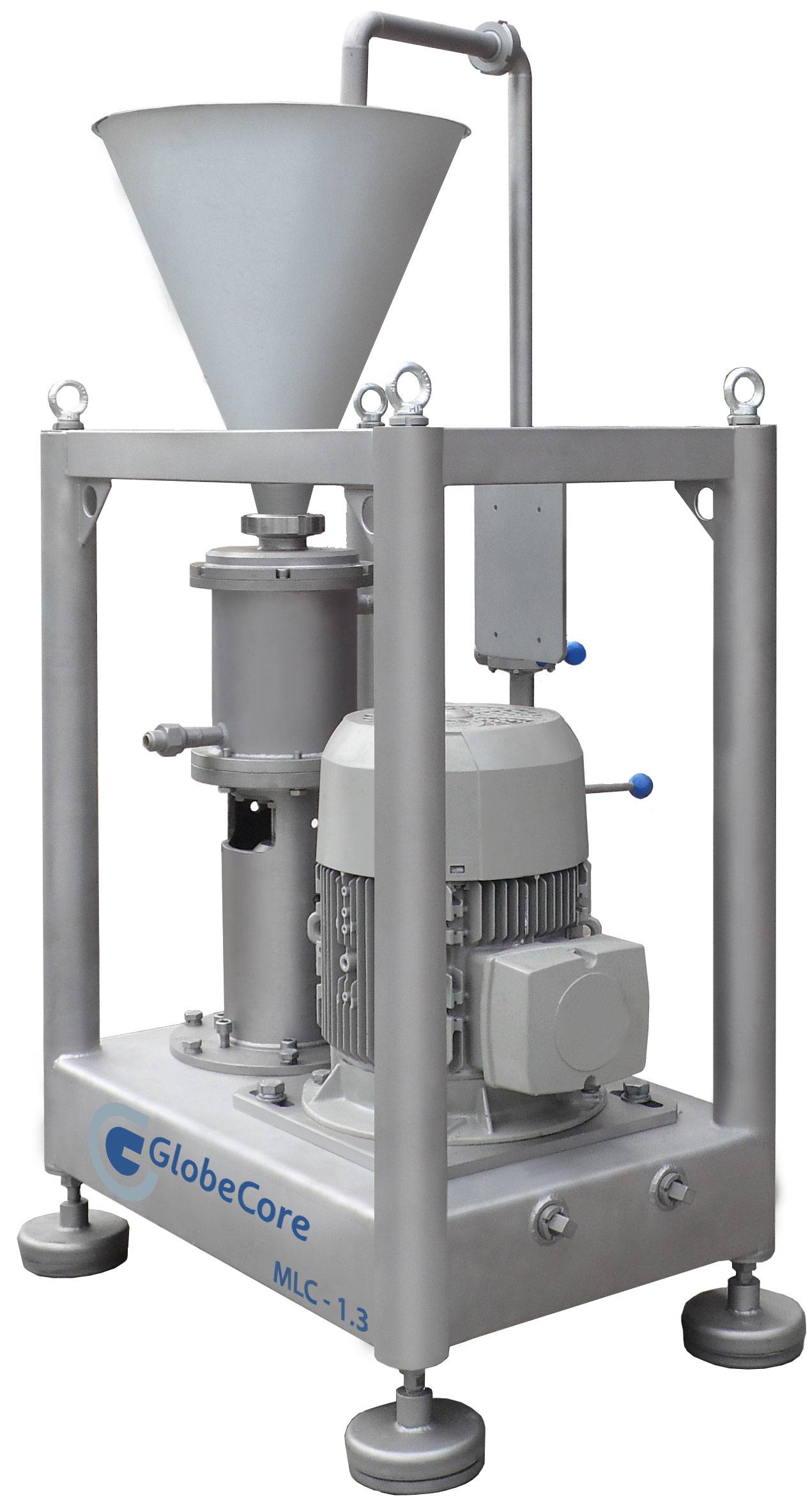
Laboratory homogenizer for sample preparation is an important piece of equipment that makes foods with new flavors, produces medicines and helps in chemical research.
Let’s consider the use of this device in different industries in detail. To compete in the food product market, many manufacturers develop new recipes, new products with improved flavors and longer shelf life, etc. At the stage of research it does not make sense to make the new product in industrial quantities. Simply get a small test sample and continue to work with it, exploring the taste and other factors. A mini-homogenizer, or more precisely, a laboratory model fits this job perfectly. Normally such equipment is smaller in size and capacity, but functions just as an industrial unit.
In the pharmaceutical industry the mass production of medicinal emulsions also starts after medicine undergoes the necessary tests and certification procedures. Here again a laboratory homogenizer prepares samples, which are then tested for effectiveness of the drug.
Generally, chemical laboratories are small areas, where research takes place in a confined space and there is simply not enough room to accommodate large homogenizing equipment for intensification of chemical reactions. And a laboratory homogenizer is big enough to obtain new materials and chemical patterns with relatively small amounts of reagents. For this purpose and for sample preparation, GlobeCore offers the CLM laboratory homogenizer. This unit uses “wet milling” principle to produce highly stable colloidal solutions, extremely fine suspensions, mixtures and emulsions.
The high quality of homogenization is achieved through an integrated use of a variety of effects and phenomena: the turbulent force (created by a complex micro-relief surface of the rotor), the centrifugal forces, the high relative speed between the rotating rotor and fixed stator, cavitation, and others.
GlobeCore colloid mills homogenize and disperse the product. Thermal jacket supplies heat to the grinding zone.