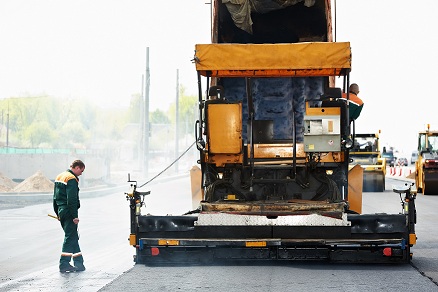
Bitumen emulsion for road construction is a colloidal dispersion consisting of two components, bitumen and water that do not blend.
The emulsion for road construction is made by the dispersion of bitumen in water solvent of emulsifier.
The performance characteristics of the latter influences the process of bitumen emulsion production. One way (direct) is that bitumen is dispersed in water. The other one (reverse) is that drops of water are distributed in the bitumen.
In the road construction industry, bitumen emulsion is more desirable because of its relatively low viscosity. The name of this emulsion, bitumen emulsion for road construction, gives us a rough idea of the fact that this emulsion is used for paving or treating road surfaces such as repairing potholes and providing a tack coat for the road base.
There are many production methods as well as applications for bitumen emulsions. The emulsion for road construction usually will consist of 50-70% bitumen, 30-50% water and 0.6 to 1.6% emulsifier. The exact mix will depend on the application and the recipe.
Emulsification of bitumen can be realized by using special equipment. In producing bitumen, the components are mixed by means of a colloid mill or ultrasound hydrodynamic cavitation.
The usage of an ultrasound system for blending is unique ans special. The system is based on ultrasound hydrodynamic cavitation. This system is used to make solution homogeneous by means of pressure fall and the separation of bitumen particles.
Additionally, this equipment also operates according to a colloid mill principle with a minor load. The advantages of such a blending of emulsions are as follows: (1) exact metering control of the components; (2) blending cycle time reduction; and (3) non-use of blending containers that ensure a homogeneous final product.
Such performance characteristics such as safety, environmental friendliness and service life extension should be mentioned while speaking about the advantages and quality of the bitumen emulsion itself.
It is therefore, bitumen emulsion for road construction that enjoys a wide popularity in many branches of the economy. The performance characteristics listed above can be supplemented with the following: (1) no need to warm up the mixture before using; (2) possibility to work with this emulsion at a low temperature (up to +5°C/41º); (3) fire prevention; (4) energy and labor cost reduction; (5) compatibility with multiple kinds of solid materials; (6) better adhesion to mineral materials owing to the emulsifier; and (7) less discharge of pollutants into the air.