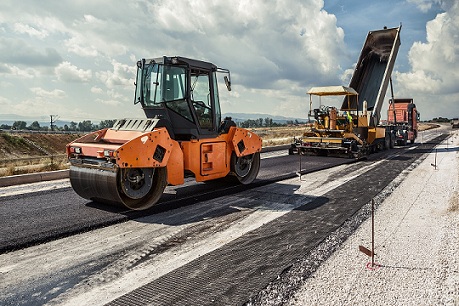
Bitumen is an important adhesive component of mixtures used in road construction projects. This substance is used only in a liquid form therefore, it must be subjected to heating.
As much as 70% of bitumen emulsion is made of the solid substance called bitumen. The particles of the bitumen are suspended in water. Additionally, bitumen emulsion retains all of its binding properties even at room temperature.
When used in paving, bitumen emulsion properly adheres to aggregate surfaces. The electric charge of the aggragates however, can damage the mixture’s balance. In order to avoid damage to the mixture’s balance, special additives (bipolar molecules of emulsifier) provide the adhesion qualities of bitumen emulsionand prevent any damage to the mixture’s balance. The bitumen particles become free from the emulsifier in order to avoid any electrolytic imbalance. As a result, bitumen emulsion is stabilized and can properly cover the aggregate surface.
The water in the mixture is forced out and evaporates because of different charges between the emulsifier and the aggregate surface. This method of ‘binding’ the construction material and bitumen (in the bitumen emulsion) improves the quality of road pavement and gives it greater strength and resilience.
Bitumen emulsion is a homogeneous adhesive liquid consisting of bitumen and water. There are also other kinds of bitumen emulsion modified by rubber fillers and high tech additives.
Distinctive performance characteristics of bitumen emulsion allows road builders to increase the pavement’s strength and drying rate. Additionally, the performance characteristics listed above enable equipment operators to use the mixture in poorly ventilated or indoor areas without any risk to human health or risk of fire.
Different bitumen emulsion equipment operates according to the principle of blending bitumen with water, emulsifiers and high tech additives. This method ensures compliance with local laws and regulations.
Batch and continuous blending machines have similar construction, but there is a difference in the blending process (double-pass or continuous blending procedures). Water, bitumen, emulsifiers and other additives are blended in a colloid mill of the batch type unit. This kind of equipment allows the operator to manage the process manually. The metering of components however, may require semi-automatic or automatic controls to reduce the risk of operator errors.
In continuous blending unit, emulsion is blended in a container with separate metering pumps for each type of material introduced to the mixture.
Bitumen emulsion is mainly used in the road construction industry, but improved composition of bitumen emulsion gives it the possibility of being used indoors to protect sanitary facilities and waterproof commerical and residential buildings.
GlobeCore GmbH designs and produces modern and efficient equipment for producing bitumen emulsion products for the road and building construction industries. Learn more about GlobeCore by visiting our website at globecore.com