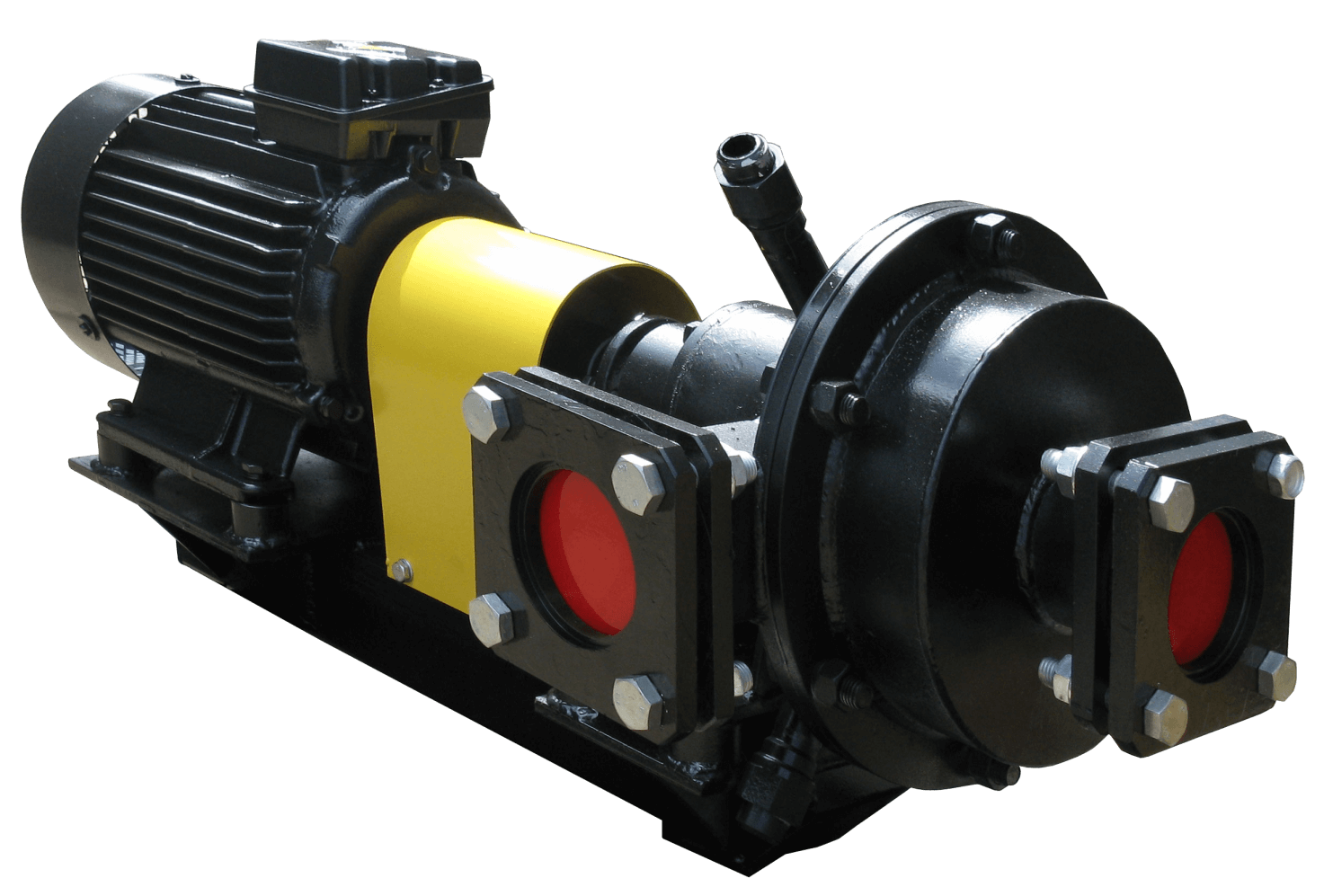
GlobeCore manufactures advanced mills for superfine grinding, able to make powders, suspensions, sols and stable colloid solutions, as well as other highly dispersed materials. One of the most widespread materials made by superfine grinding is water-bitumen emulsion, widely used in road construction, water proofing of buildings and roofing. GlobeCore specializes in manufacturing of UVB type equipment, made specifically for water bitumen emulsion production.
The superfine grinding mills are made for intensive dispersion of mineral or chemical raw material. Such mills work with low and medium hardness materials and are used in chemical, pharmaceutical, metallurgical and construction industries. Superfine grinding mills are ball crushers, planetary and bead mills, as well as colloid mills and vortex layer generators.
Dispersion in the superfine mills occurs either in batches or continuously, wet or dry. In a dry mill, grinding occurs in air or in inert gas medium by crushing and grinding of the raw material into superfine substance. Dry grinding allows to use larger particles of the raw materials, since the impact action of the balls is more efficient than wet grinding. At the same time, wet grinding mills and in more demand for preparation of colloid solutions and other dispersed systems. New advanced technologies by GlobeCore ensure superfine grinding of organic and inorganic materials on nanometric scale.
Most devices designed for superfine atomization of raw materials, can be designed for both wet and dry grinding. Such are ball crushers, which employ the impacts, caused by rotation of the drum and constant motion of the materials inside: balls of steel, cast iron or another durable material. Ball crushers can be manufactured on industrial or laboratory scale, and can have one or two chambers. Such devices is a prototype of planetary mills, which feature several drums rotating simultaneously around a central axis and their own axis as well. These devices are significantly more efficient in terms of impact on the processed material. Planetary mills offer high degree of dispersion of suspensions and powders.
Bead mills and colloid mills are designed for preparation of highly dispersed material in water media: superfine suspensions, highly stable emulsions and colloid solutions. While the colloid mill dispersed the materials by intensive contact of the rotor and the stator, the bead mill works by constant impacts of beads with the particles of the material.
Complex processes occur in the cylindrical drum of the vortex layer generator between the ferromagnetic particles, the raw material and the liquid, moving in a rotating magnetic field and forming a vortex layer. The advantage of this system is that such interaction accelerates the atomization of the material, increasing production efficiency. The generator can also be used as a reactor to intensify chemical processes.