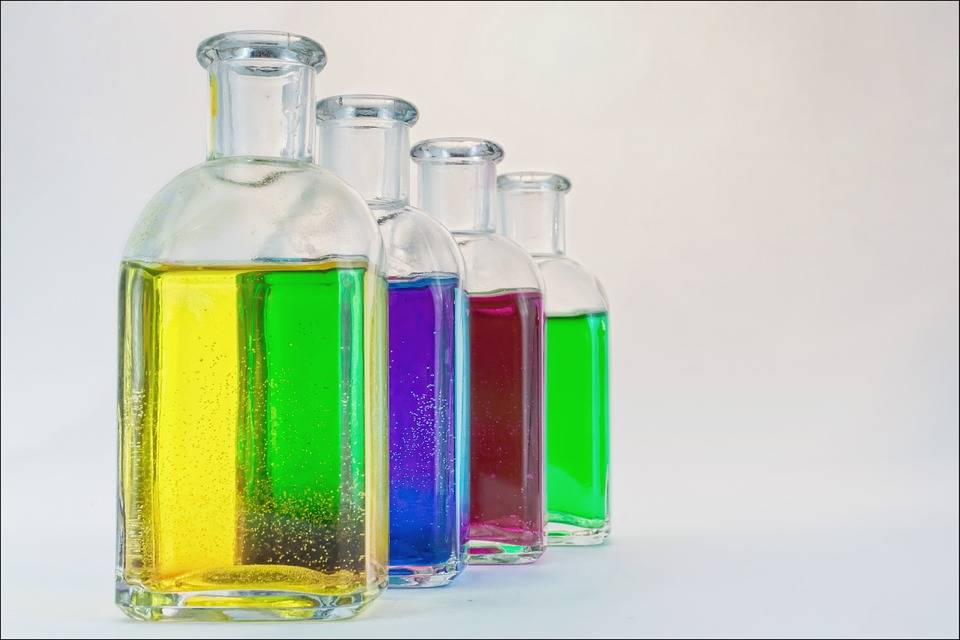
Medicine in liquid form released over the counter are obtained by mixing or dissolving the active ingredients in various solvents: ethanol, water, oils, etc. There is also an alternative method of manufacturing medicine in liquid form – extracting active ingredients from plant products.
The basic requirement for such medicine is dispersed and homogeneous distribution of the active substance in a liquid dispersion medium
The classification of liquid forms is based on the degree of grinding of the active substance and the nature of its connection with the dispersion medium. There are 4 liquid forms:
- Emulsion;
- Suspension;
- True solutions;
- Colloidal solutions.
Also available are medicines that are combinations of the above types of liquid forms. They are extracts, infusions, tinctures, etc.
The reasons for the wide use of liquid medicine
Biopharmaceutical research proved that the use of liquid medication has a more pronounced effect on the process of healing. In addition, liquids have a number of other advantages, among which:
- Simplicity and ease of use;
- Faster absorption;
- Masking unpleasant taste and odor;
- Variety of use.
Production of liquid forms of medicine
Production of liquid medicine is based on the mixing process. Mixing achieves the homogeneity of medicine distribution in the dispersing medium
The CLM colloid mill by GlobeCore disperses the chemicals in a liquid medium in a process called “wet” grinding. Also, there are other forces that enhance the impact in the colloid mills by GlobeCore; cavitation, mashing and centrifugal force between rotor and stator changing particle size.
The CLM colloid mills make highly stable and ultra-fine medicinal emulsions, suspensions and solutions, which do not separate during prolonged storage and retain their healing properties.